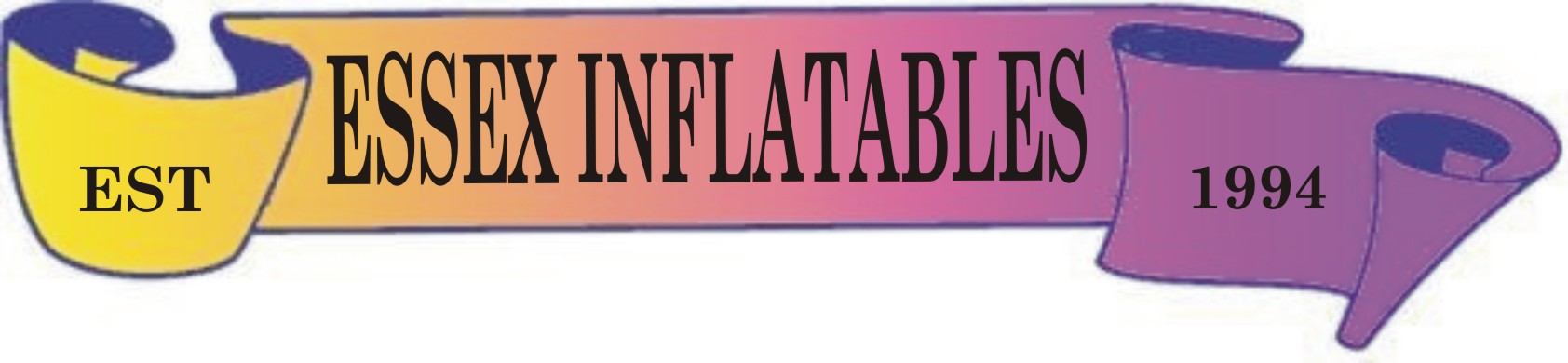

The Information below is a summary put together by tipe an organization that Esses Inflatables highly recommend
Operators Guide To Annual Testing
Introduction:
To test or not to test is probably the question most operators ask themselves at
some time or other and many still do not understand why an annual test is a legal
requirement
In 2006 the European Parliament passed EN 14960 which has been accepted by the UK and comes
under the British Standard Institute (BSI) and has the number BSEN 14960:2006. This document
covers the manufacture, operation and testing of inflatable play equipment that is ‘jumped’ or ‘slid’ on.
This British Standard is NOT law but is the only document appertaining to the manufacture, operation
and testing of inflatable play equipment available to the industry. IPMA/AIMODS members and most
UK manufacturers now build to this Standard.
Operators who hire or allow members of the public to use equipment are required to ensure that their
equipment is ‘safe for purpose’ and this is covered by the Health & Safety At Work etc Act 1974
(HASAWA) and the Provision of Work Equipment Regulations 1998 (PUWER). Both of these regulations
ARE law.
HASAWA, Section 3 (2) states “It shall be the duty of every self-employed person to conduct his
undertaking in such a way as to ensure, so far as is reasonably practicable, that he and other persons
(not being his employees) who may be affected thereby are not thereby exposed to risks to their
health or safety.”
It is this requirement that all companies have to comply with and the section that prosecutions are
usually made.
To assist bouncy castle companies complying with this, HSE produced ETIS 7.
ETIS 7 states:
“Inspection, maintenance and modification
The Provision of Work Equipment Regulations 1998 (PUWER) require inflatable devices to be inspected
at suitable intervals to ensure that safe conditions are maintained, and that any deterioration in the
device is detected and remedial action taken in good time. (See following paragraphs on annual
inspections and daily checks.)
Annual inspection
Each inflatable should be thoroughly inspected at least once in every 12 months. This procedure needs
to be carried out by a competent person.
The Annual inspection needs to include checks of the following:
· previous inspection reports and certificates where appropriate;
· provision of a blower unit as specified by the manufacturer, or one that at least provides sufficient
pressure to allow the inflatable to be used safely, suitably guarded at the air inlet and outlet;
· condition of blower impeller and fan casing where practicable to inspect;
· condition of accessible blower electrical wiring;
· condition of all electrical installations;
· anchorage system for wear, rips or chafing;
INFORMATION SHEET 33
2
•type and number etc of ground anchors or ballast for conformity with design specification;
· structure for wear or rips in the fabric;
· walls and towers (when fitted) are firm and upright;
· pressure is sufficient in the bouncing area and at the step/front apron to give a reliable and firm
footing;
· internal ties for wear and tear, particularly at loose or exposed ends;
· bed seams, wall-to-bed seams and wall-to-tower connections;
· identification of the device; and
· if used on a fixed site, the location.
Inspection of some of these features may need to be done inside the device. The above list is not
exhaustive and the manufacturer may specify additional items. Annual inspection needs to include any
part of the inflatable and its ancillary equipment that may affect the safe operation of the device.
Daily checks
Checks should be carried out before the first use on any day using advice provided by the
manufacturer in the operations manual. These should include checking that:
· the site remains suitable, with crowd control measures in place if appropriate;
· anchorages are intact, protected where necessary, and ropes not worn or chafed;
· anchor system secures the inflatable device to the ground;
· there are no significant holes or rips in the fabric or seams;
· the correct blower specified for the device is being used and the air pressure is sufficient to give a
reliable and firm footing;
· there are no exposed electrical contacts, there is no wear on electric cables, and plugs, sockets and
switches are not damaged;
· if an internal combustion engine is used, that the fuel cap is placed firmly on the fuel tank and any
reserve fuel tank is suitable and remains in a safe position;
· bolts and screws of the blower are properly secured and that robust guards are secured over the air
inlet and outlet;
· the blower/inflation tube connection is in good condition and is firmly fixed to the blower; and
· the blower is positioned correctly, adequately protected or guarded and is not causing a tripping
hazard.
The public should not use the inflatable until any defects identified in the daily check have been
rectified.”
BSEN 14960:2006 states :
“7.1.1 Routine inspection
The controller shall carry out, or appoint a person to carry out, routine inspection.
Routine inspection shall be carried out before use each time the equipment is to be made available
for use. The check shall include that:
- site is suitable;
- all anchorages are secure and in place;
- ancillary equipment is in position (e.g. impact-absorbing mats);
- there are no significant holes or rips in the fabric or seams;
- correct blower is being used;
- internal air pressure is sufficient to give a firm and reliable footing;
- there are no exposed electrical parts and no wear on cables;
- plugs, sockets, switches etc. are not damaged;
- connection tube and blower are firmly attached to each other;
- blower is safely positioned and its mesh guards are intact.
The equipment shall not be used by the public until any defects identified in the routine inspection have
been rectified
3
7.1.2 Annual inspection
The controller shall ensure that an annual inspection is carried out by an inspection body which shall
include any part of the inflatable and its ancillaries, which may affect safe operation of the equipment.
It shall include checks of:
- previous inspection reports and certificates where appropriate;
- identification of the inflatable and blower (e.g. serial numbers);
- anchorage system for wear, rips or chafing;
- type and number of ground anchors or ballast for conformity with the design specification;
- inflatable structure for wears or rips in the fabric;
- walls and towers (when fitted) for firmness and uprightness;
- internal air pressure to be sufficient to give a reliable and firm footing;
-internal ties for wear and tear, particularly at loose or exposed ends;
-bed seams, wall-to-bed seams and wall-to-tower connections;
-mesh guards at the inlet and outlet of the blower;
-condition of the impellor and fan casing;
-condition of electrical wiring and/or installations;
-presence of the fuel cap (petrol - engined blowers)
Inspection of some of these items may need to be done inside the inflatable. The above list is not
exhaustive”
It should be understood that ETIS 7 was revised at the time when the draft of EN 14960 was being
discussed and takes many of its points from EN 14960 (now BS EN 14960:2006)
The bottom line is that whilst PIPA, RPII and BSEN 14960:2006 are not legal requirements HASAWA
and PUWER ARE law and therefore so is annual testing of inflatables.
HSE have also stated that operators who use either the ADIPS or PIPA schemes for their annual test
will be deemed to have followed ‘best practice’. It follows that operators who use ADIPS or PIPS for
their testing are covered in the eyes of the law. The confusion lies in the fact that HSE state that other
methods can be used to comply with HASAWA and that tests should be carried out by a ‘competent
tester’. Operators need to understand that if they choose to have their units tested outside of ADIPS or
PIPA it will be their responsibility to prove the competence of their tester should the need arise. We
would suggest that any operator deciding to test outside of ADIPS or PIPA should at least use an RPII
registered inspector. It would not be enough to say that a tester could be considered ‘competent’
because he/she has ‘x’ amount of years experience. It is almost certain that HSE or others would
demand an independent evaluation to determine ‘competence’.
In a successful prosecution of an inspector in May 2009 HSE used BSEN 14960:2006 as part of that
prosecution under the HASAWA. It is possible that this could set a legal precedent in any future cases.
In effect making BSEN 14960:2006 law.
Operators should only purchase new equipment that conforms to BSEN 14960:2006 and ensure that
the documentation issued with the unit clearly states this.
Disclaimer: This document is for general guidance and research purposes only, and does not purport to give
professional or legal advice.
Sources:
Inflated News Play & Attractions / TIPE / Health & Safety Executive / BSEN 14960:2006 / ETIS 7 / HASAWA
May 2009
|